Excessive heat can stall the performance of components such as drilling motors and rotary steerable systems, dramatically shortening their life spans. Heat-damaged electronic components can silence data collection and communication in the downhole environment, increasing rig non-productive time and equipment repair costs.
TUNDRA™ MAX land mud chillers are closed-loop refrigeration systems designed to cool drilling fluids even under extreme conditions. A portable, computer-controlled, dual-stage mud chilling system cools high-temperature mud in a two-stage process.
Within normal temperature ranges, drilling fluid protects downhole equipment and maintains optimal performance. Extreme temperatures degrade mud properties, creating issues such as increased mud loss, thermal instability, and inconsistent rheology measurements. Mud performs best at lower temperatures, saving the cost of additives or replacement.
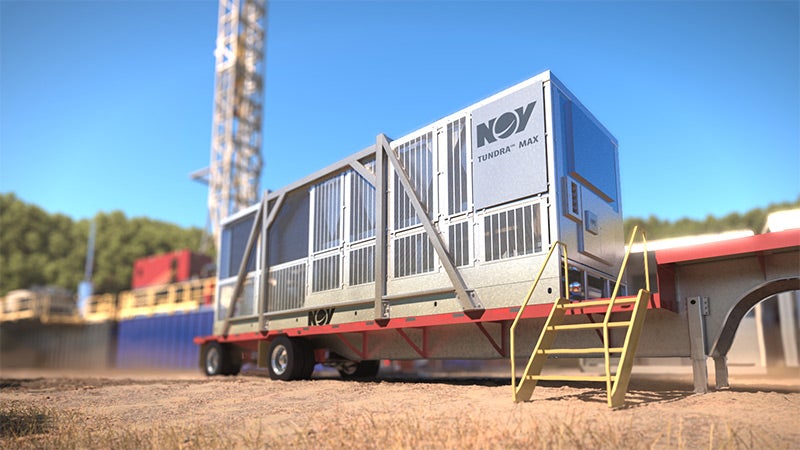
Cooler drilling fluid prevents heat-related equipment failures and recoups time throughout the drilling process. Stable downhole temperatures reduce the time needed to recondition mud returned from the wellbore. This speeds up the process to reoptimize mud formulas for downhole temperature fluctuations, all while providing better wellbore stability.
TUNDRA MAX performs when conventional cooling methods fail. Air cooling is slow, inefficient, and highly dependent on ambient temperatures. The dual-stage cooling system can actually reduce the temperature of processed drilling fluid to below the ambient air temperature.
Air systems have limited value in regions with extreme climates. This is especially true in places like the Middle East, where temperatures can climb above 120 °F (49 °C). Water-based cooling systems require a local water source—an uncertain commodity at some remote land drilling sites.
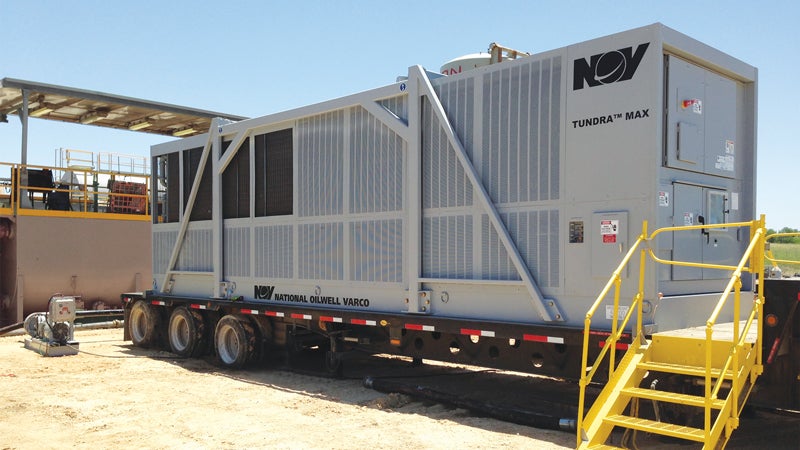
In 2015, a detailed field study in the Eagle Ford shale tested how well TUNDRA MAX could reduce drilling fluid temperatures at a high flow rate with a small footprint. The study compared wells in South Texas equipped with advanced drilling automation tools, both with and without the mud chiller. The analysis included drilling speed, efficiency, and downhole tool operational safety.
The well not using the mud chiller logged two temperature-related downhole tool failures, causing significant downtime. When TUNDRA MAX was activated on the second well, the operator reported zero temperature-related failures. A reduction in downhole tool trips alone allowed the well to be drilled 2 days faster than the previous well.
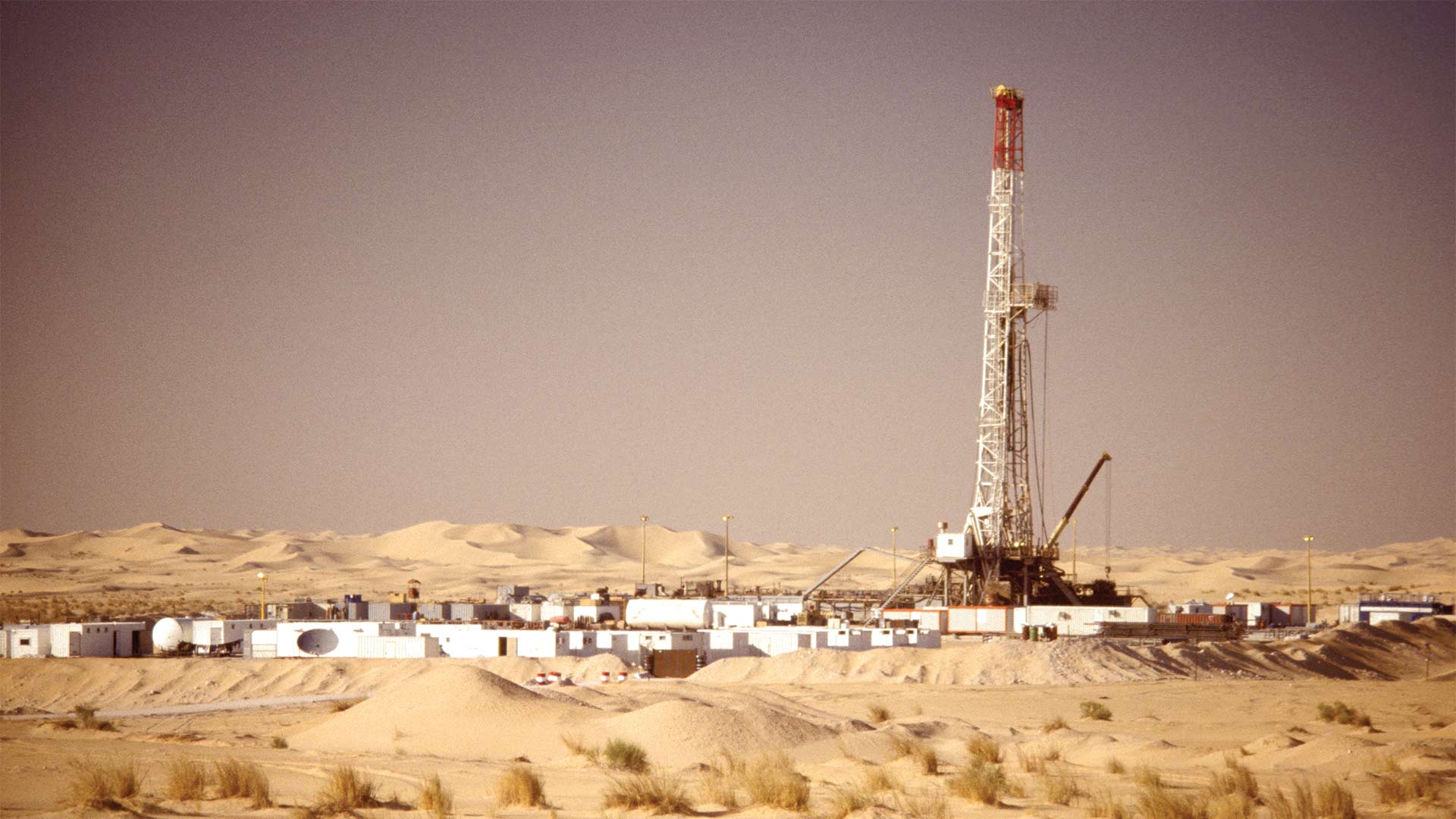
In this same study, the battery on the high-speed downhole dynamics measurement tool achieved 240 of 250 hours of maximum battery life. This unprecedented 44% increase—up from 167 typical hours—was credited to TUNDRA MAX reducing bottomhole temperature by 22 °F (12 °C).
Superior cooling reduced the amount of circulation required to lower the temperature of the well. The cooler environment gained an additional 1,000 ft (305 m) before equipment-damaging temperatures were encountered. Drilling restarted sooner and saved 51 hours of nonproductive time.
Well operators in southern Louisiana have also confirmed the high performance of TUNDRA MAX. The mud chiller was enabled on a well at 16,900 ft (5150 m), reducing the temperature gradient by 15% and saving 28 hours of temperature-related downtime.
TUNDRA MAX mud chillers eliminate dependence on local air and water conditions while extending equipment life and increasing drilling performance. These tough, efficient units are giving well operators a faster, more reliable way to beat the heat.