Traditionally, only measurement-while-drilling (MWD) drilling tools have given operators knowledge of what is happening downhole, with no option for a similar tool for completion-liner deployment. The i-Con™ string-dynamics logging tool addresses this need, providing data from deployment of lower completions and liner-hanger assemblies to give insight into what is happening in the well. The tool records tension, compression, torque, temperature, and internal and external pressure. Once retrieved from the hole, data obtained by the i-Con tool can be easily downloaded and investigated to improve understanding of downhole and surface measurements. In addition, the tool has a full-bore ID, enabling compatibility with liner-hanger systems to allow cementing plugs to pass.
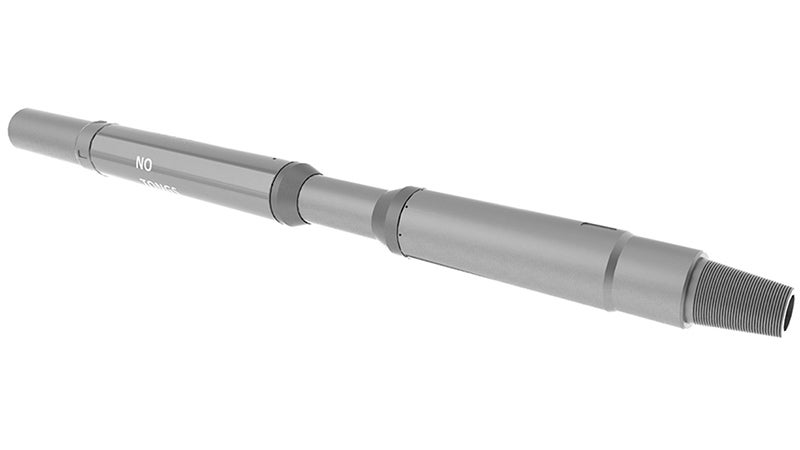
The i-Con string-dynamics logging tool provides data from deployment of lower completions and liner-hanger assemblies to give insight into what is happening downhole.
An independent operator was planning a major 11-well field development in the North Sea that included installation of long, 4½-in. completion liners. Successful completion-liner deployment was identified as a major risk and, despite the expected positive impact of using managed-pressure-drilling techniques, a strong understanding of downhole dynamics during liner deployment remained a challenge. This issue was compounded by the fact that the new campaign included significantly longer laterals than previous campaigns, with complicated lithology, varying pore pressures, and openhole stability concerns.
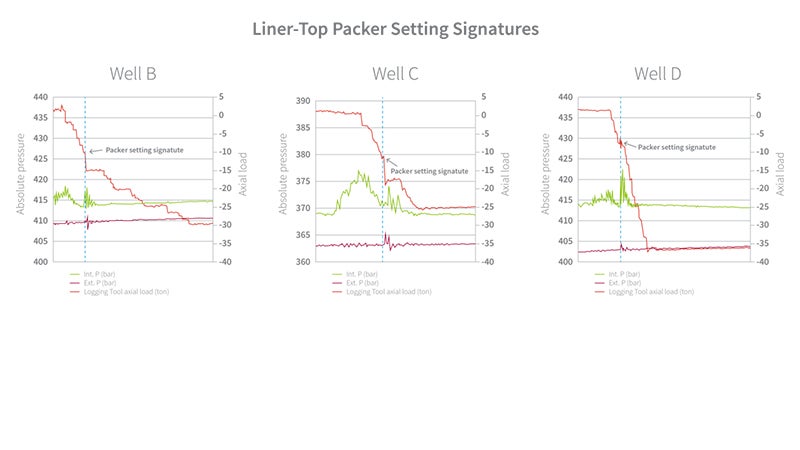
This graph shows downhole weight and pressures, recorded packer setting, and total set-down weight during setting of liner-top packers in the field-development campaign.
The i-Con tool was made up directly above the liner-hanger running tools to continuously record downhole data during each liner run. Data recorded during the project, which in total exceeded 27 days of operational time in the well, provided input to confirm torque modeling and friction to improve liner-deployment parameters for rotating liners. The downhole data at the liner top provided valuable information to refine the modeling of liner connections and downhole completion tools when it became necessary to rotate the liner and work it to bottom. Accurate and detailed axial-load data near the liner-top tools confirmed the successful and unsuccessful setting of liner-top packers, and when a packer began leaking early in the project, procedures were updated with revised slack-off loads and all subsequent packer installations were successfully set and tested.
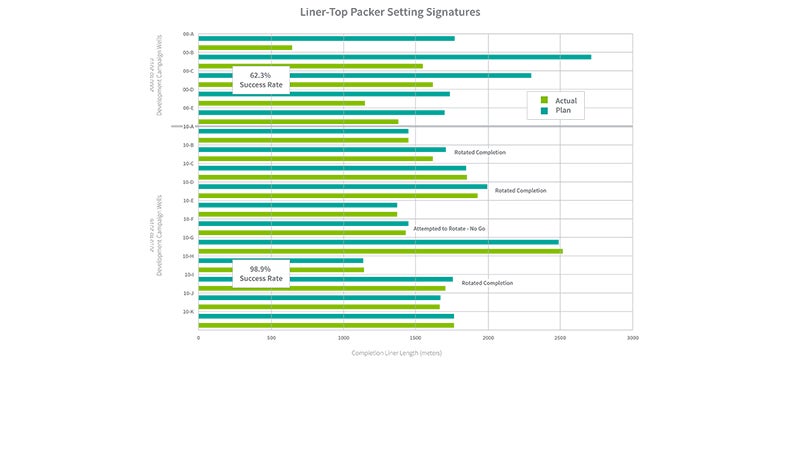
In combination with drilling and completion design improvements on the front end of the project, the improved understanding of downhole dynamics related to liner deployment played an important role in the success of the field development campaign.
The data obtained were used to facilitate the optimization and continuous improvement of liner deployment operations to allow the drilling and completion team to overcome a steep learning curve. The operator was also able to establish best practices and troubleshoot unexpected issues more effectively because of the data. By focusing on achieving planned total depth (TD) with the lower completion liner and developing an active learning strategy to optimize deployment throughout the campaign, the logging tool made it possible to successfully overcome past challenges and achieve planned TD in most wells.
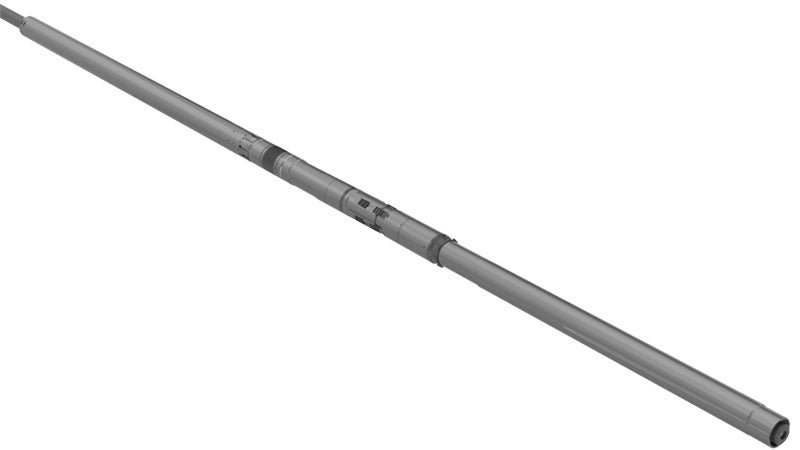
The i-Con tool records a variety of measurements downhole, including tension, torque, compression, temperature, and internal/external pressure.
Over the 11-well program, the operator was able to reach a success rate of 98.9% for planned completion-liner TD, an increase of more than 36% over previous campaigns. The accurate downhole data obtained allowed the operator to improve their operations, prevent failures, and reduce nonproductive time (NPT). NPT saw particularly substantial reductions in the second half of the wells, which were delivered efficiently despite being the most technically challenging wells of the campaign. Continual improvements in design and operational parameters further contributed to this success and helped the operator develop lessons learned for implementation in future campaigns.
Understanding downhole dynamics presents a wide range of benefits to oil and gas operators. This project allowed NOV to demonstrate that optimization of operations, even in challenging applications, is possible with innovative equipment and the expertise to properly implement a solution.