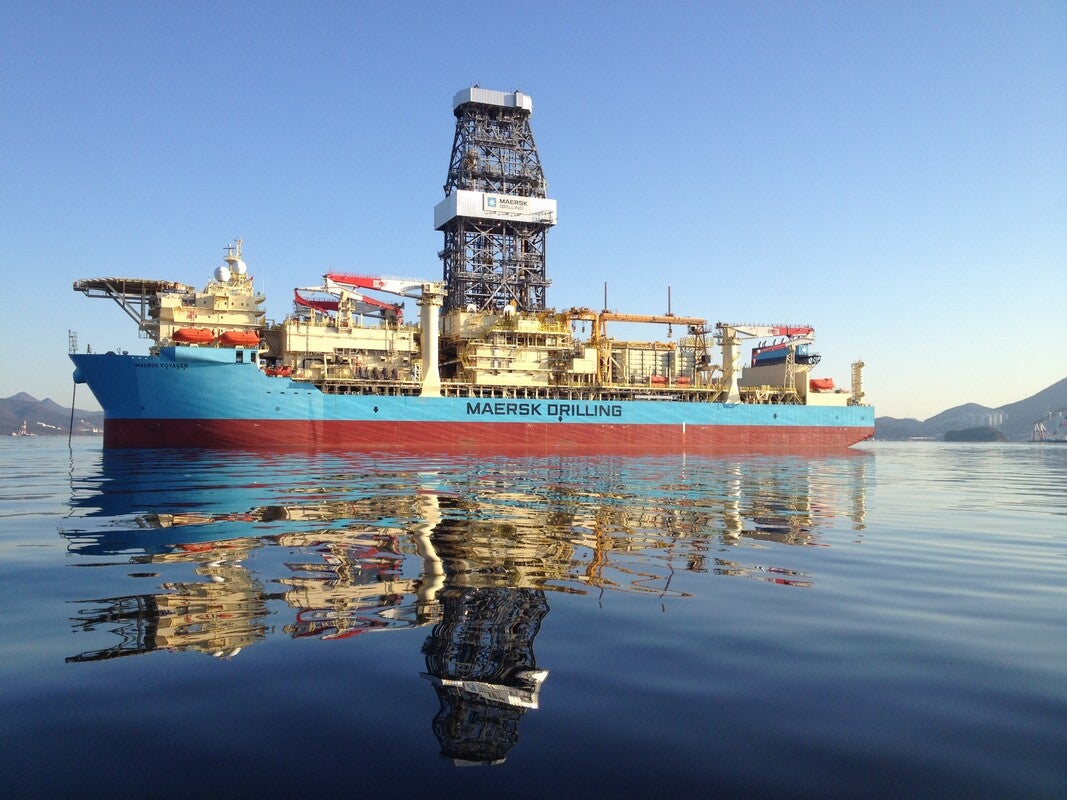
There is a suite of challenges that the oil and gas industry has faced during the COVID-19 pandemic. Day-to-day tasks that are critical for our customers to complete have been severely impacted by several factors such as travel restrictions and quarantine requirements. It is through these challenges that we have worked with our customers to find ways to help their operations continue.
Most recently, we were contacted by Maersk Drilling who needed the drill floor workbasket that we refurbished and shipped to them to be installed, commissioned, and certified on the Maersk Voyager drillship located offshore Angola. This job typically requires an NOV field service technician (FST) to travel to the rig; however, sending an FST to the rig with the turnaround time needed along with the travel restrictions and quarantine protocols was not feasible.
That is where our TrackerVision™ real-wear technology came in to play. NOV service technicians are typically the ones equipped with the TrackerVision technology that enables them to stream real-time audio and video to our subject matter experts (SMEs) at our global service centers to view what is happening in the field, provide guidance, and streamline troubleshooting. Since an FST couldn’t travel to the rig, we were able to work with Maersk Drilling to send them a TrackerVision kit so that in this unique situation their employees on the rig could use the technology to communicate with an NOV SME at one of our global service centers in Port Elizabeth, South Africa.
Electrical Supervisor for the Maersk Voyager, Jacob Ostergaard, stated, “The advantage of being first-movers in remote commission and support is that we in Maersk Drilling together with our partner NOV are setting new standards within the industry. This is a new standard not only during COVID-19, but also for the future of offshore.”
The Maersk Drilling employee was able to use the TrackerVision technology so that the NOV SME could visually inspect the equipment via real-time streaming while also talking the Maersk Drilling employee through the step-by-step process for startup and commissioning of the workbasket. This made it possible for the NOV SME to see exactly what the Maersk Drilling employee was seeing while providing instantaneous directions and next steps. A benefit of utilizing the technology’s augmented reality functionality was verifying the correct e-stop to be commissioned. The NOV SME was able to remotely highlight the e-stop on a user manual and then send that image to the Maersk Drilling employee’s headset. Once received, the employee was able to use the TrackerVision headset to view the user manual on top of what he was seeing on the rig and easily identify the correct e-stop. The real-time streaming and feedback allowed for everyone to avoid the lengthy process and potential delays that come with trying to email or call back and forth from the rig to the service center. By utilizing the TrackerVision technology we were able to effectively save Maersk Drilling 54% of what the job would have cost by eliminating travel, visa, and quarantine costs.
“Industry collaboration is a key ingredient to a sustainable future. All facets of industry talent, from the manufacturer to the end user need to work together to deliver a cost-effective product and service. This philosophy was put to the test on Maersk Voyager and proved effective. Close cooperation between Maersk Drilling, the customer, and NOV enabled a successful project through virtual communication and technology,” says Douglas Marks, Technical Section Leader, Maersk Voyager.
While this is not the typical process for inspecting and commissioning equipment, this is a way of the future. NOV is fully equipped to help assist and ensure our customers succeed in whatever way possible. For this specific instance, both NOV and Maersk Drilling worked together to address the challenges that they faced and were able to complete the job in just four days—enabling operations to continue uninterrupted.
To learn more about TrackerVision and NOV’s other remote support capabilities, click here.