Up to 50% more oil can be tapped by increasing reservoir pressure via water injection and other methods. Global water injection requirements are projected to double or triple within 10 years, with offshore drilling creating much of this demand.
Removing sediment and bacteria from injection water is never cheap, and moving the process offshore only increases complexity. Oil and gas companies rely on preliminary well test information to estimate oil reserves and production rates before investing in costly topside water treatment systems. Even tiny miscalculations can lose millions of dollars. "Life-of-field" water injection requirements rarely match initial expectations, particularly if satellite fields are discovered and processed via the same offshore infrastructure.
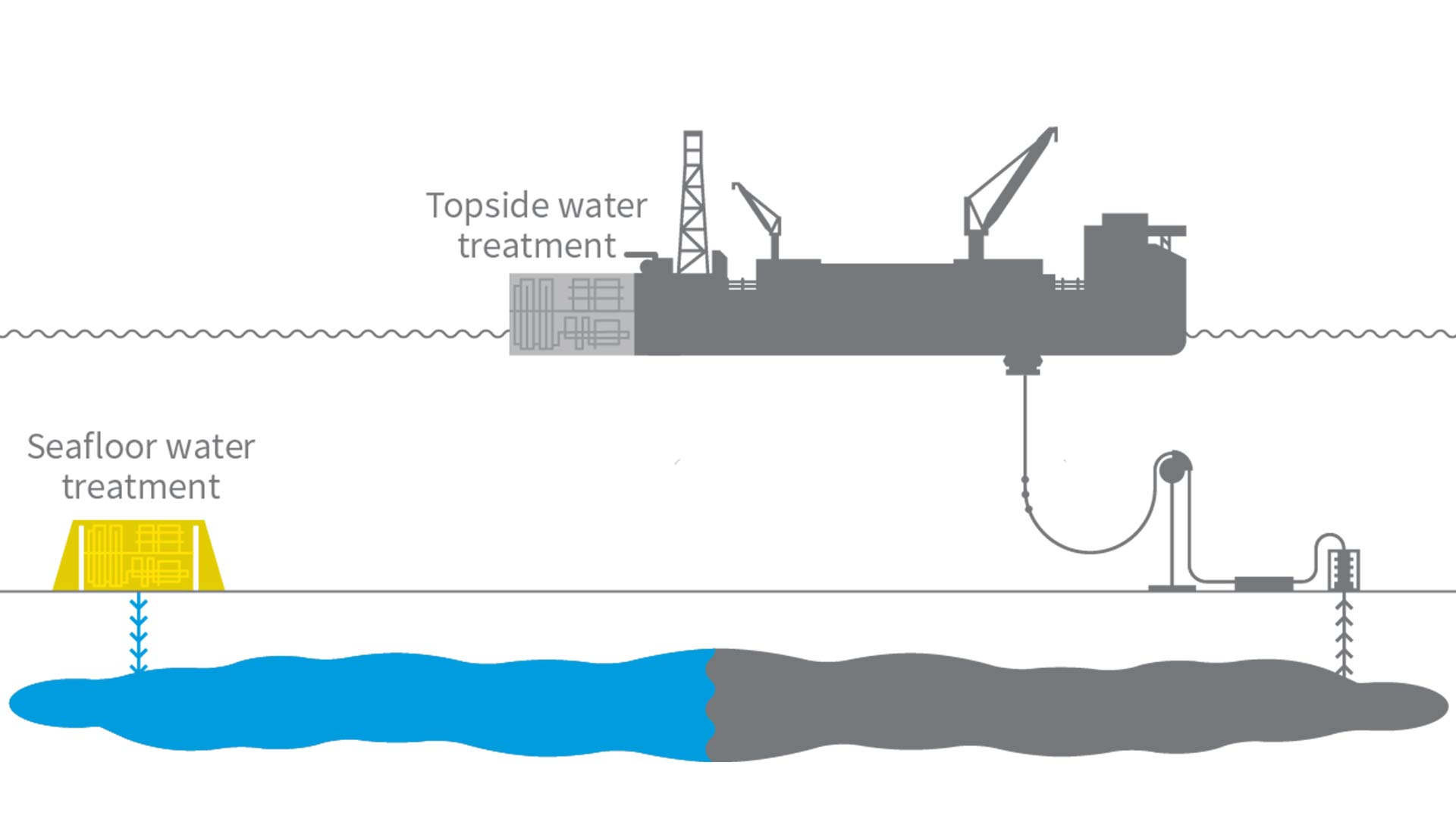
The Seabox™ SWIT™ technology offers a flexible solution that moves offshore water treatment from topside to seafloor while providing exceptionally clean injection water. This approach saves the cost, weight, and space issues of topside systems and offers a modular approach to water treatment planning. Operators can adjust field drainage strategies as they go, reducing the uncertainties of planning traditional treatment systems within an industrial megaproject. This gives greater flexibility to optimize field drainage during or after investing in the infrastructure, aiding recovery of larger volumes of reserves.
At depths of less than 500 ft (152 m), offshore production platforms are commonly fixed to the seabed. Deeper water requires self-contained capabilities such as floating production storage and offloading vessels and tension leg platforms. Traditional topside treatment requires bulky equipment costing up to $70,000/ton (/tonne) and weighing thousands of tons (tonnes). These units require large amounts of deck space, leaving little flexibility for change as reservoir knowledge evolves during production.
Imagine the Seabox SWIT technology as a structure that sits on the seabed and uses an injection pump to draw seawater through it. Disinfection chemicals such as chlorine and hydroxyl radicals are generated via electrolysis on their way through specially designed cells, removing the need for liquid chemicals or moving parts. The convoluted path and long residence time inside the box remove solids via sedimentation and provide a chlorine soak that thoroughly kills bacteria. The system can be scaled to any volume requirement, producing injection water with quality far superior to that of topside systems.
Subsea water treatment allows reservoir engineers to inject as much water as they need—when and where they need it—without relying on topside infrastructures. The system increases flexibility by relocating treatment units on the seabed, allowing injection to continue independently of platform production shutdowns.
The lack of moving or rotating parts supports a proven record of 99.8% reliability, compared with 85% for most surface-based seawater injection systems.
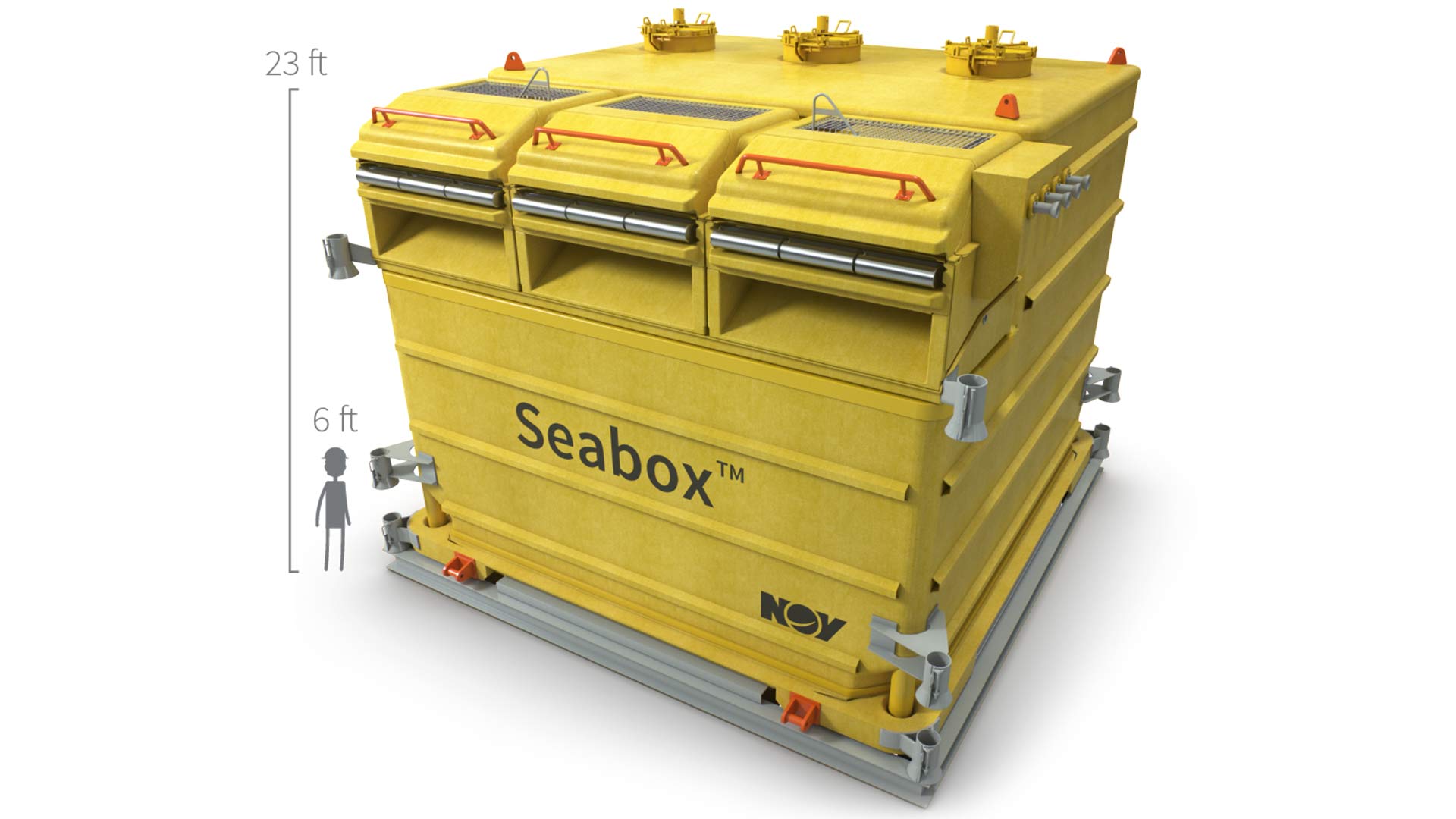
The large-volume still room weighs 47 tons (43 tonnes) and contains a removable "treatment unit" with a maintenance window of up to 4 years. The system only requires electrical power for the electrolysis and control systems, with a design life of more than 20 years. The lack of moving or rotating parts supports a proven record of 99.8% reliability, compared with 85% for most surface-based seawater injection systems.
Major multinational oil companies have acknowledged the Seabox SWIT technology as fundamental to adding incremental water injection with minimal facility preinvestment, allowing flexible adjustments to reservoir drainage strategies for the lifetime of a field. The technology offers significant environmental and safety benefits that include lower power requirements, no liquid-dosed chemicals, zero chemical handling, and reduced offshore manning requirements.
Far below the surface of the ocean, Seabox will quietly transform top-heavy water treatment into a lean, green, maintenance-free machine.