As horizontal wells become more prevalent globally and as vertical wells reach greater depths, operators face more friction along the drill string, which frequently leads to stick/slip situations. Common in North America, these well profiles are spreading into the Middle East, increasing the odds that operators in this region will encounter the same challenges.
Across six continents, the patented axial oscillation technology of the Agitator system has provided unparalleled downhole friction reduction to improve drilling performance in conventional and unconventional wells. With more than 70,000 successful runs, Agitator systems have delivered tens of thousands more successful runs than any other friction-reduction tool in the oil and gas industry. Compared to other industry offerings, the Agitator system provides up to 200% better rate of penetration (ROP) and as much as 50% less weight on bit (WOB). The elastomer power section is incredibly durable, logging a proven reliability rate of 99.9%.
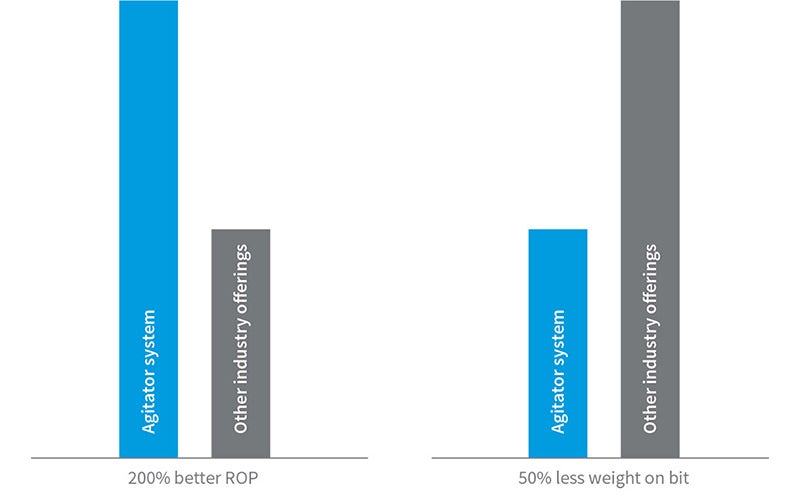
In directional drilling operations, friction forces work against the bottomhole assembly (BHA), causing poor weight transfer to the drill bit. This can lead to pipe buckling, which results in lost drilling time. The type of oscillation makes a significant difference downhole. The Agitator system uniquely reduces the friction forces by providing axial oscillations, which provide greater friction reduction benefits than tools that create lateral vibration. Forward-and-backward axial motion travels a greater distance up and down the drill string. The benefit of lateral motion is much more localized in comparison.
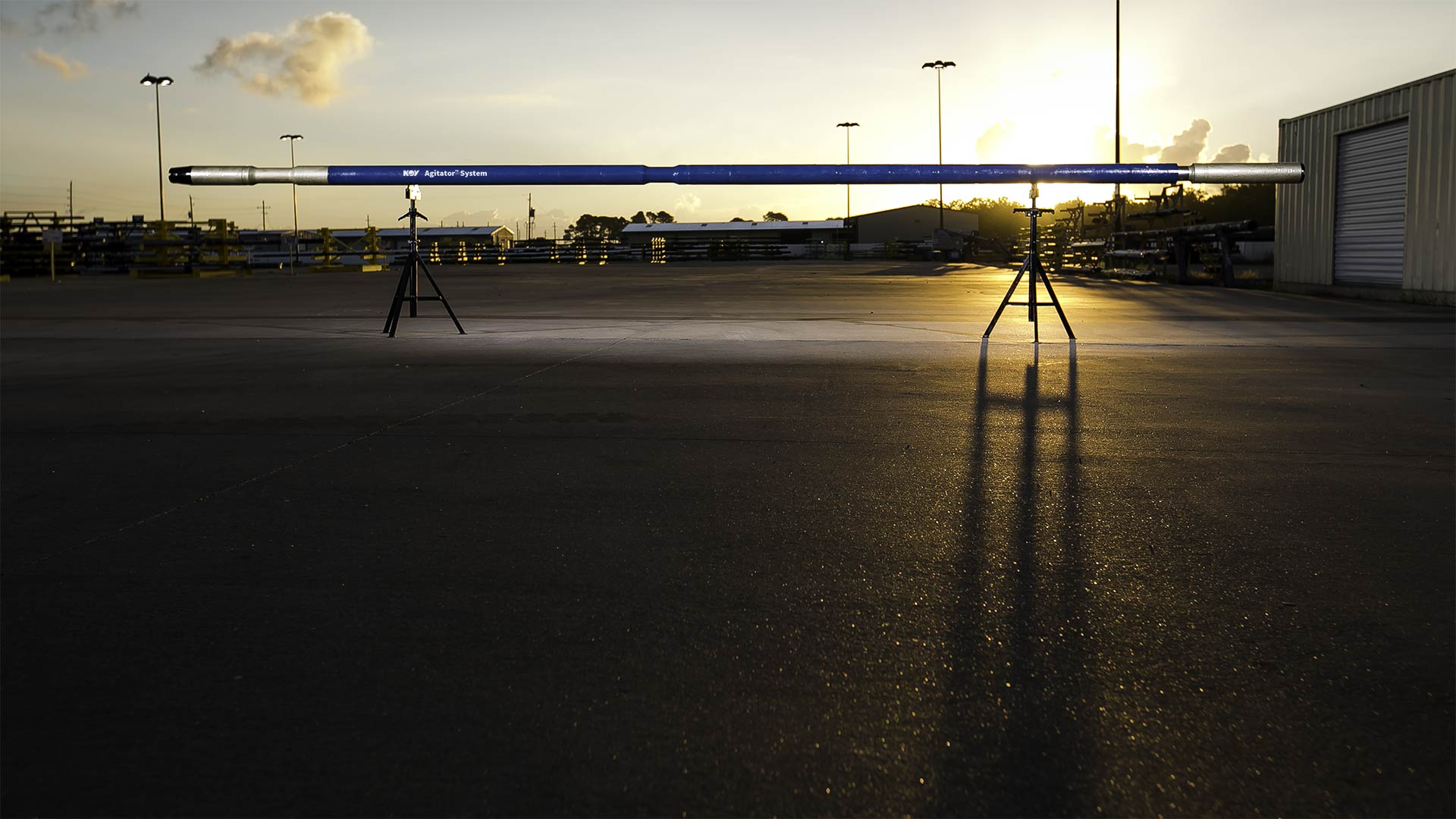
To envision how axial oscillation works, imagine a cell phone setting on an incline. When the phone is not vibrating, it stays stationary. Once a call comes in and the phone begins to vibrate, it slides down the slope. The movement breaks the friction between the phone and the surface it is resting on, allowing the force of gravity to overcome the friction forces. The same principle works on a drill string resting on the bottom side of a borehole in an extended-reach operation.
Incorporating the Agitator system into the BHA has enabled operators around the world to reduce friction and drilling time, saving operating costs. In Egypt, an operator experienced torque and drag challenges when drilling in complex wells. Using a 6¾-in. Agitator system improved WOB and allowed the operator to drill an entire 8½-in. section in one run. Compared to offset wells without the Agitator system, the drill string with the Agitator system saved half a dozen trips, increased average ROP by 31%, and reduced cost per foot by 42%, saving an estimated $580,000.
An operator in West Texas used the Agitator system to reduce fluctuations in WOB and differential pressure on two wells, resulting in improved ROP and tool-face control. The Agitator system reduced drilling time by 50% and saved an estimated $100,000.
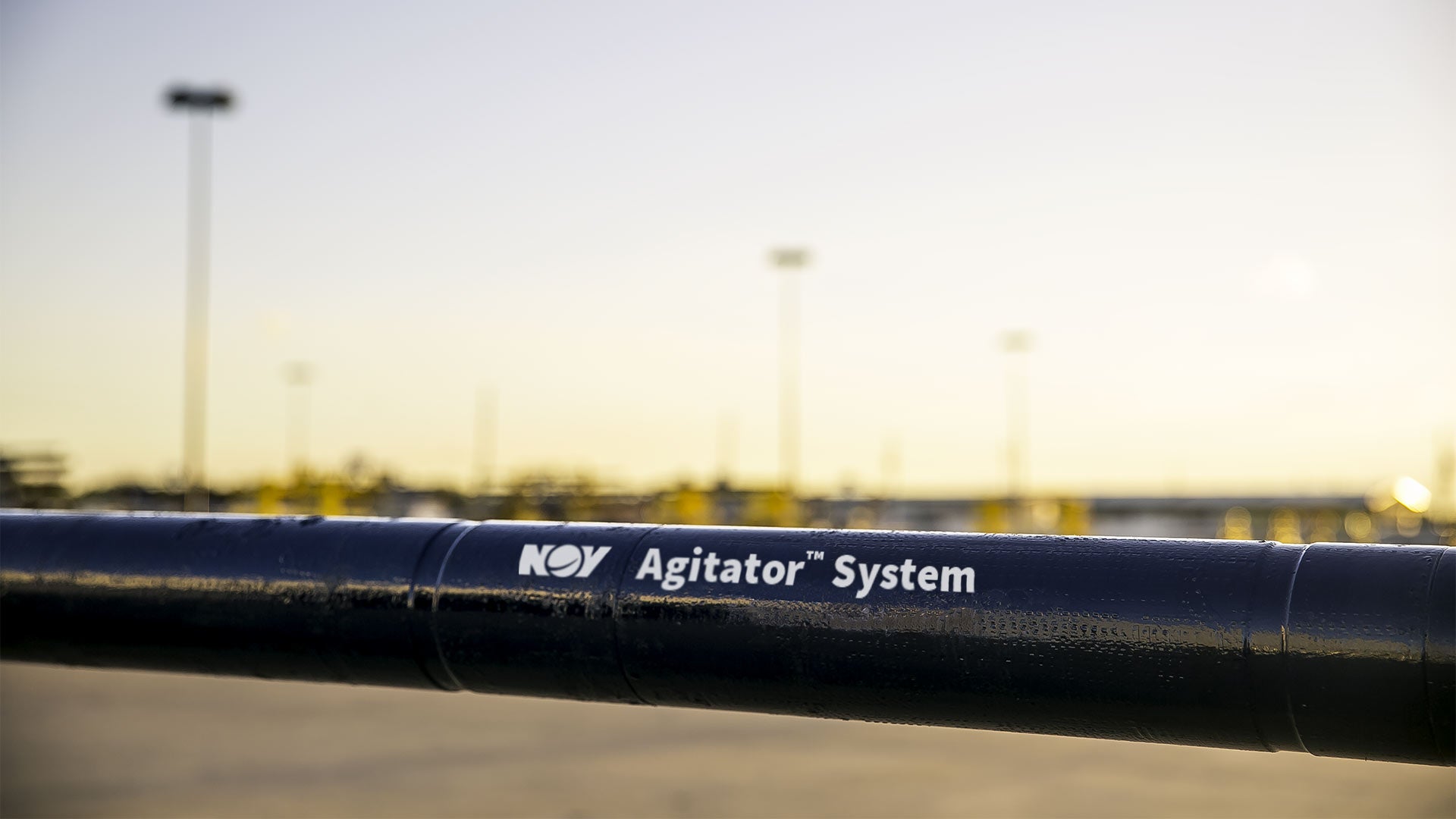
In Mexico, one customer wanted to compare rate of penetration of a well drilled with an RSS to one drilled with an RSS and the Agitator system. Adding the Agitator system to the string resulted in a 100% faster ROP compared to the best offset well that ran an RSS alone.
Another customer in Mexico compared the results of drilling a well with an RSS to drilling with an Agitator system instead. In this case, the well with the Agitator system improved ROP by 222% compared to the offset well using the RSS.
Today's oil and gas landscape demands that operators drill faster and farther than ever before. Agitator systems break through friction and move operations along a path toward higher profits.