As oil wells in the region have aged they have become richer in water, which creates a bottleneck for end users; to produce one barrel of oil, for example, an operator would need to handle two or three barrels of water which will make the liquid separation operation very difficult as there is a limited holding capacity in the wet tanks. The aging wells and depleting reservoirs in the Middle East often see a water cut, or the ratio of water produced compared to the volume of total liquids produced from an oil well, as high as 75%. Excess water production can cause a host of technical and economic problems, which has driven a shift in implementation of water management technologies in the region.
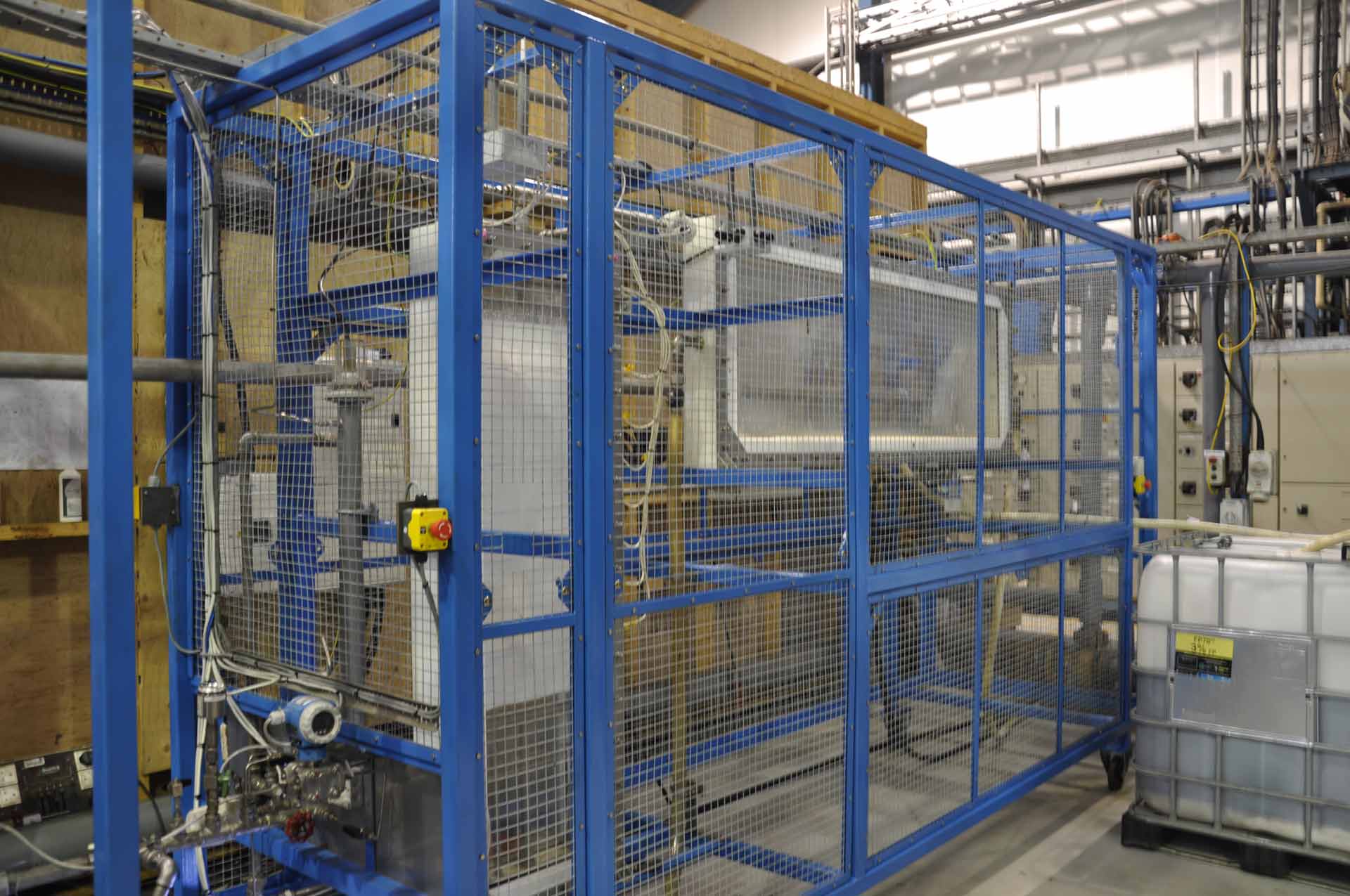
A Compact Electrostatic Coalescer (CEC™) is encased in a cage for testing.
Several clients in the region determined that a water management solution was necessary to address these issues, and specifically requested a technology that receives fluids directly from the wellhead via headers and processes them in a very compact manner to prepare oil for export. Most of the product received by their production units—giant facilities that have capacities of more than 200,000 bbl of liquid per day—is an emulsion, meaning that the liquid/liquid separation cannot be achieved using exclusively enhanced gravity separators. The typical solution for breaking the emulsions, the application of heat, is often not feasible for this application due to various cost and footprint restraints; furthermore, such heating systems could often be complicated and difficult to operate.
NOV developed a unique Compact Electrostatic Coalescer (CEC™) technology unit that meets the demands of operators facing tight emulsion productions. The CEC applies electrostatic fields to the emulsion, causing the water droplets to vibrate, shake, and collide with other water droplets. This allows the water to separate out from oil and other elements and eliminates the need for costly, hard-to-use heating systems. The fabrication phase for these projects have already begun, with NOV to supply the CEC as well as all the other required separation vessels and internals and several other proprietary technologies to achieve the overall process guarantees as part of an overall Oil and Water Treatment Scheme in the first quarter of 2018. NOV will continue to be present from late 2018 onward for commissioning and start-up, operating jointly with the operators to ensure that the projects run at optimum efficiency at that the equipment consistently works as expected.
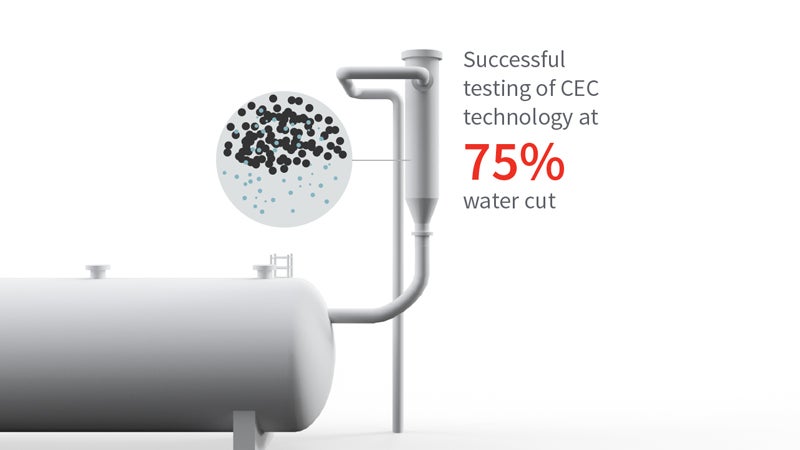
The projects’ first major success was to reduce the footprint of the main equipment by 25% versus the original layout specifications set forth in documents during the Conceptual and Tender phases. Furthermore, using the CEC reduced the amount of auxiliary equipment—piping, valves, structures, electrical cabinets, and so on—necessary to continuously and efficiently operate the plant by 60%, especially for the high CRA materials (duplex stainless steel or higher). In wells producing oil with high water cuts, the cost of handling water can often dramatically increase lifting costs; having the CEC, which went through rigorous testing at our testing facility in Orkney, Scotland, and achieved success with a water cut of 75%, will prove invaluable in the long term. These technology benefits, combined with NOV’s large regional footprint versus many competitors, gave our clients the confidence necessary to choose NOV as the preferred equipment provider for the first phases of the projects.
We’re proud that our innovative technology was selected by the key operators in the region, and are looking forward to continuing our partnership on landmark water management developments in the future.